Ceramic Injection Molding is the combination of two previously established technologies: Plastic Injection Molding and Powder Metallurgy. The CIM process results in complex shaped ceramic components that can help meet the varied needs of businesses.
Ceramic Injection Molding Process
- Firstly, ceramic powder particles and a binding agent are mixed to create a homogenised mixture. This is known as the Feedstock.
- Next, the Feedstock is injected into a mold cavity to form a Green Part, which is defined as a part made of powdered material that is compressed and held together with binding material. It then undergoes a binder removal process, through either heat or chemical treatment, to produce a Brown Part.
- After debinding, the Brown Part undergoes a sintering process at a specific temperature/atmosphere profile, until it hits the targeted density. It is then left to shrink up to 15%.
CIM Materials
With the increase in market demand and customer needs, the range of material that is available in DYT grows steadily in numbers.
Among them are high purity oxide and carbides, such as Alumina and Zirconia, WC and SiC, as well as toughened Alumina and stabilized Zirconia.
Our full material list is available here.
CIM Applications
Ceramic Injection molded parts have applications in various industries, due to their ability to be shaped in complex geometries while maintaining a consistent quality.
Medical
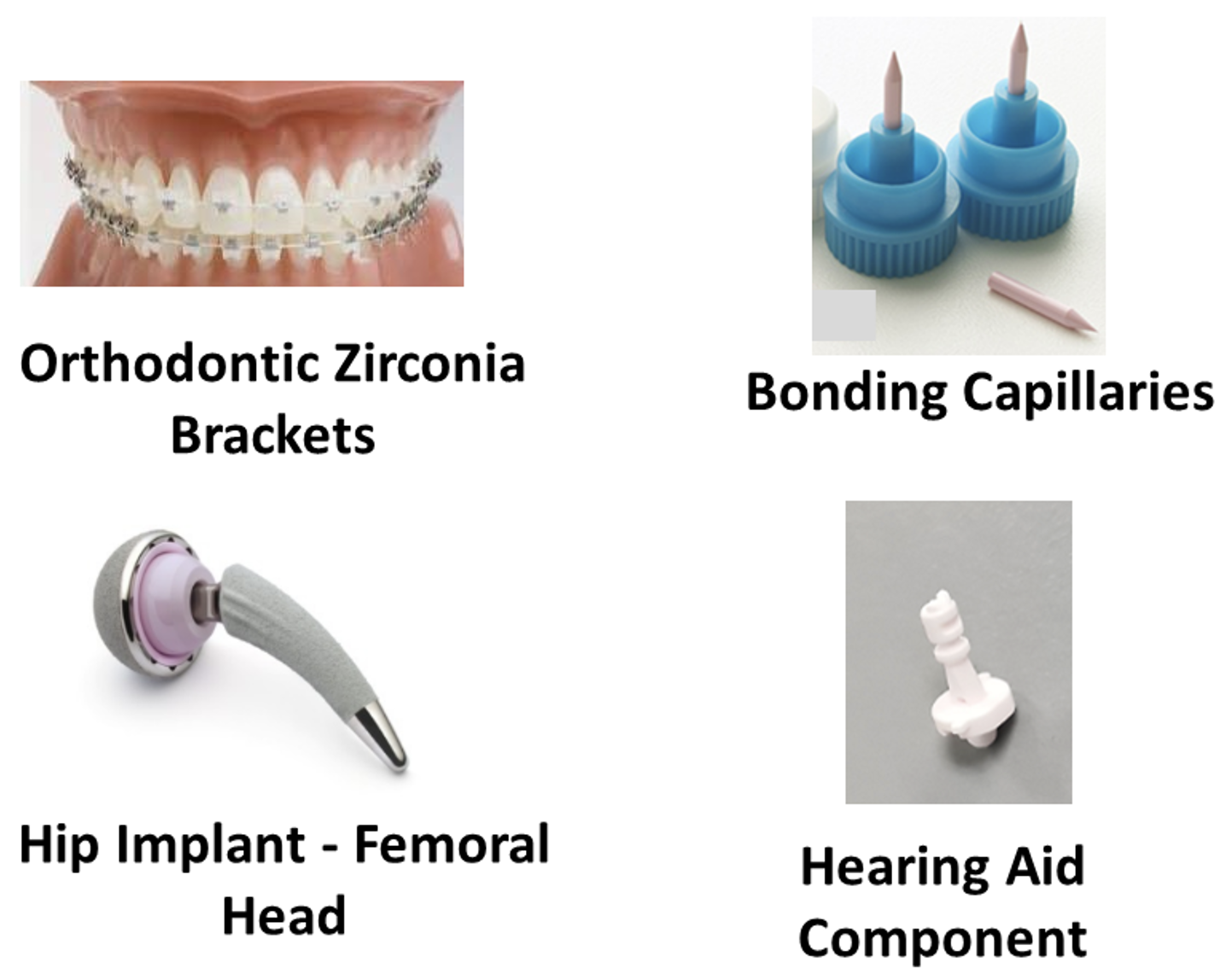
Due to ceramic material properties, CIM components offer high hardness, excellent wear resistance, biocompatibility making it suitable as implants and for use in orthodontic applications.
Consumer Electronics
Typical Normal applications are ceramic capacitors, heat insulators, ferrules for fiber optics.
Automotive
Typical Normal applications are ceramic washers, ceramic battery caps, ceramic seals for E-bike/ Bicycle Braking System.
CIM Design Guidelines
General Guidelines
Dimension Tolerances
Part Thickness Guidelines
CIM Advantages
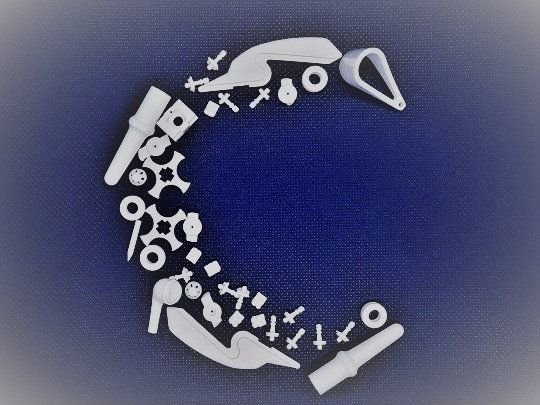
Some CIM Advantages are:
- Complex components.
- Provides unique, economical solutions to increasingly stringent material and product design requirements.
- Excellent batch to batch repeatability and process capabilities achieving tolerance of +/-0.5%.
- High Surface finish quality without the need for additional finishing processes.
- Superior material performance, high hardness and mechanical strength, wear, corrosion and weathering resistant, dimensionally stable, high working temperature and good electrical insulator.
- Can be used for metallised applications.
Discover CIM Manufacturing Solutions With Dou Yee Technologies
Ceramic Injection Molding (CIM) offers multiple advantages over conventional methods, making it an essential process for industries such as the automotive, medical, and consumer electronic fields that require high quality ceramic parts. These advanced ceramics bring flexibility, material strength, and cost efficiency, making them a top choice for manufacturers.
Dou Yee Technologies has the manufacturing capability needed to provide advanced CIM solutions and take your production to the next level. Contact us today to find out more about what we offer.
Dou Yee Technologies provides services worldwide, including direct coverage in Singapore, Germany (Dusseldorf, Stuttgart, Frankfurt), and the US (California, North Carolina). We also extend our services to many other countries and regions across the globe. Contact us today to inquire about how we can assist you, wherever you are located!
Contact us today to inquire about our services.
立即联系我们以了解更多有关我们提供的服务信息。
联系我们